Further to the last blog, after we finished all the decal works. we go to another manufacturing step. check below picture and guess what this man is doing? you see a balance, and the material on one end, on the other side, it is a certain weight used on the balance. Yes he is weighing the correct amount that is used to make one single product before pour the material into the mold. unit weight is very important to control the final product quality. overweight of the product is a waste of material and nothing good for product as well. on the contrary, shortage of weight is not able to form a correct product shape. to control it with a uniform standard, a balance is the best tool and does good better than human’s experience. Never afraid of a worker who even does not know specific weight making mistakes.
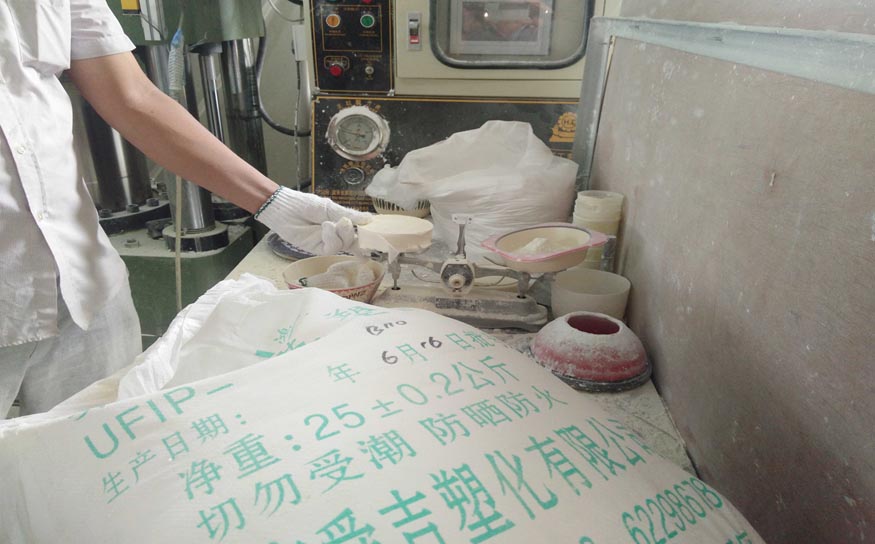
After we measured correct amount of material, we also need to put the material in a drying machine again to dry out any moisture that is still possibly existing. meanwhile a specific mold can solidify the material into a cube in case that material powder does not fly around by air fan in workshop and no bubbles or a pinhole formed in final products. this is an important procedure to control the final product quality.
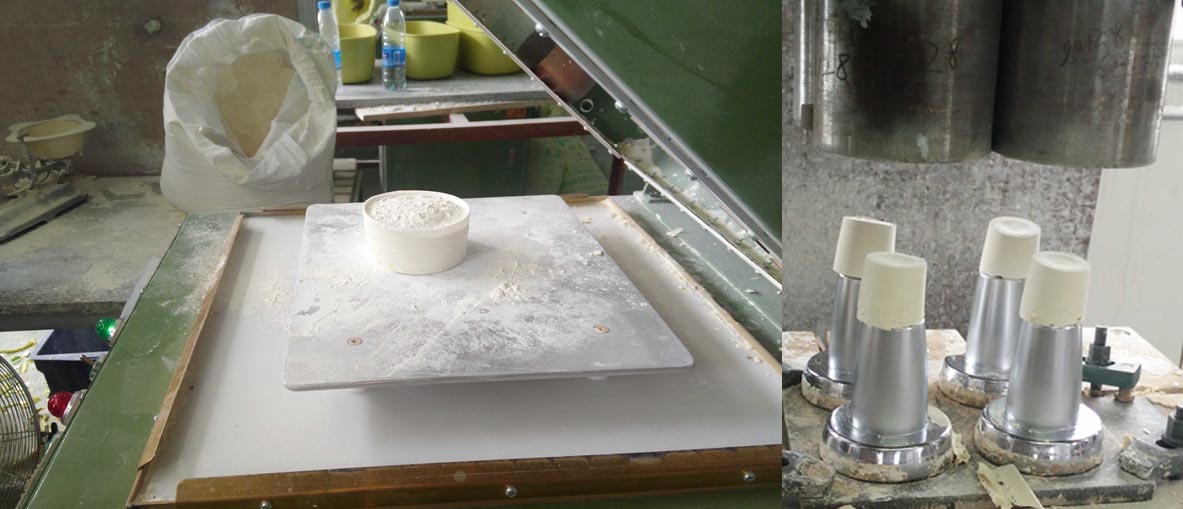
After the material has been dried out and cubed. workers use a high pressure air sprayer to blow away any dirty or material leftover in mold cavity, only everything is confirmed very clean. bamboo fiber cube will be placed in the center of the mold for next moulding/pressing.
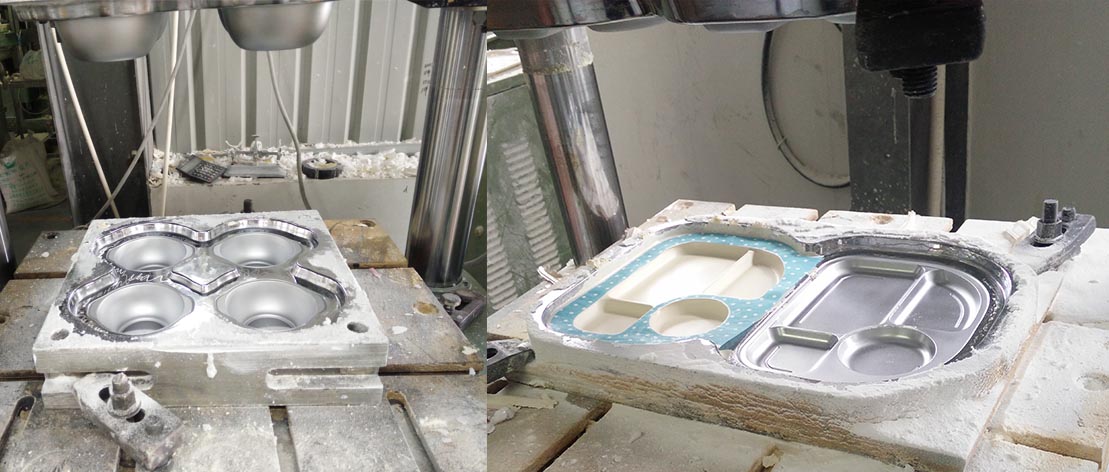
Mold Cavity/Cavities
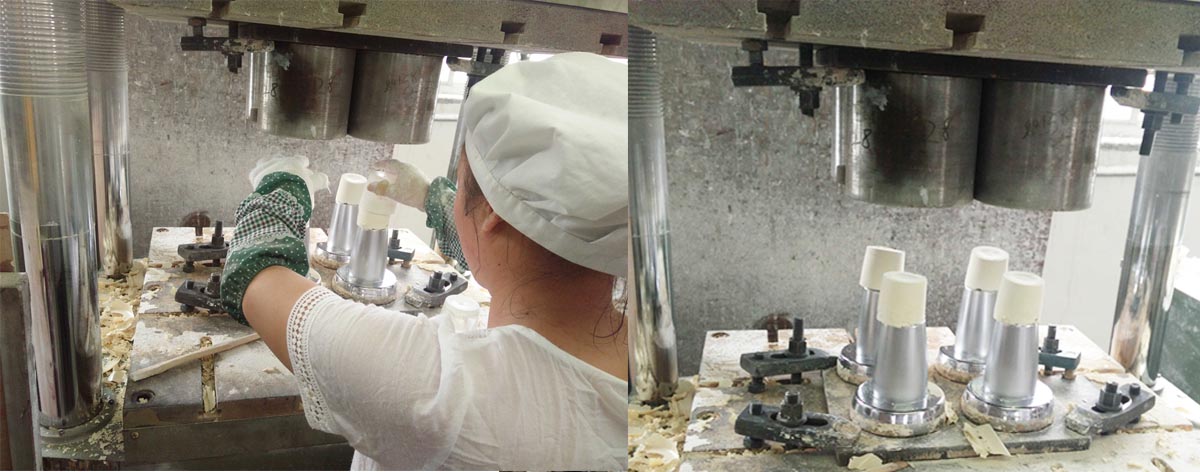
Mold pressing is an automatic process, which requires professional and technical worker to set up the mold and adjust suitable parameters to allow production operators to do normal and efficient production. In order to make full use of the resources, the machine custom made with different tonnage, large-tonnage machine produces a large product or one mould with several cavities to produce several products at once.
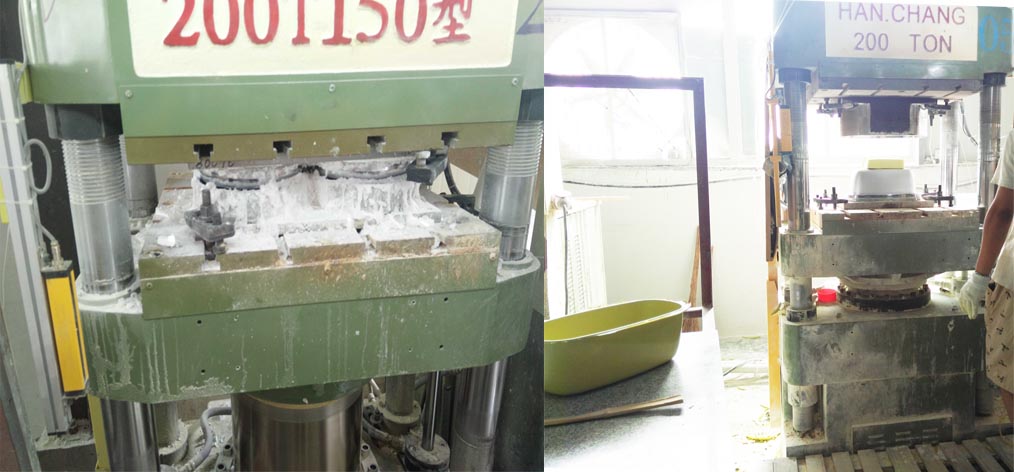
After the cube is pressed into product shape. workers need to stick the decal right away after mold leaves the cavity. the decal should be in correct position and consistent with product edge. this is a key step how to control the decal in correct position. worker should be well trained and very careful to make no mistakes. however any works that is manually controlled, it certainly can not be exactly same. even though there are many works that have been adopted to control the quality to the best. decal position is still not absolutely 100% on the same place.
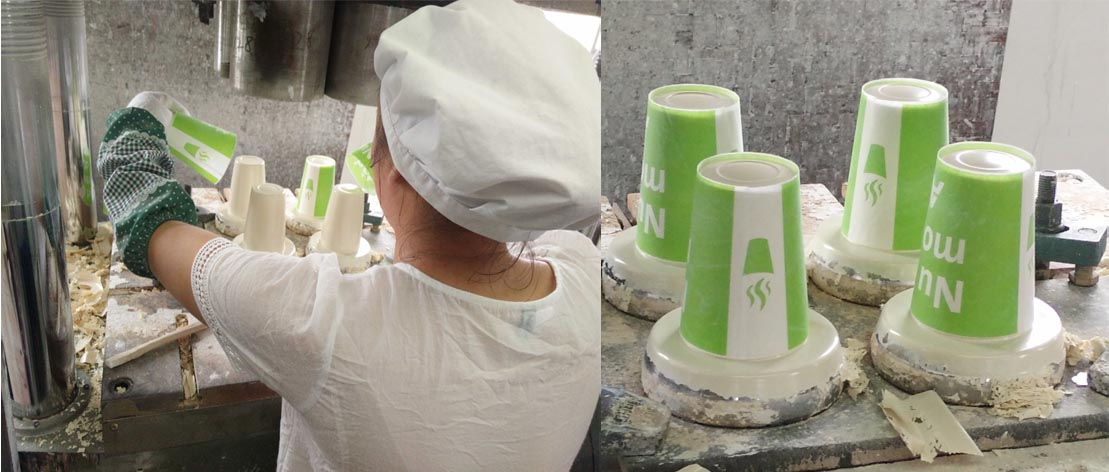
Once decal is correctly wrapped around, operators spray a small certain amount of food safe lightness powder above the positioned decal. powder should be distributed very even without any bump. so we select very skilled people to do this work. Lightness powder increases product brightness and can protect decals in mold cavity. after finish all preparations, mold will close again to incorporate decal into product by means of high temperature in mold cavity. once all is finished, a printed product will be born. and the remaining work is just to polish the extra scraps on product’s edge. This will be posted in next article.
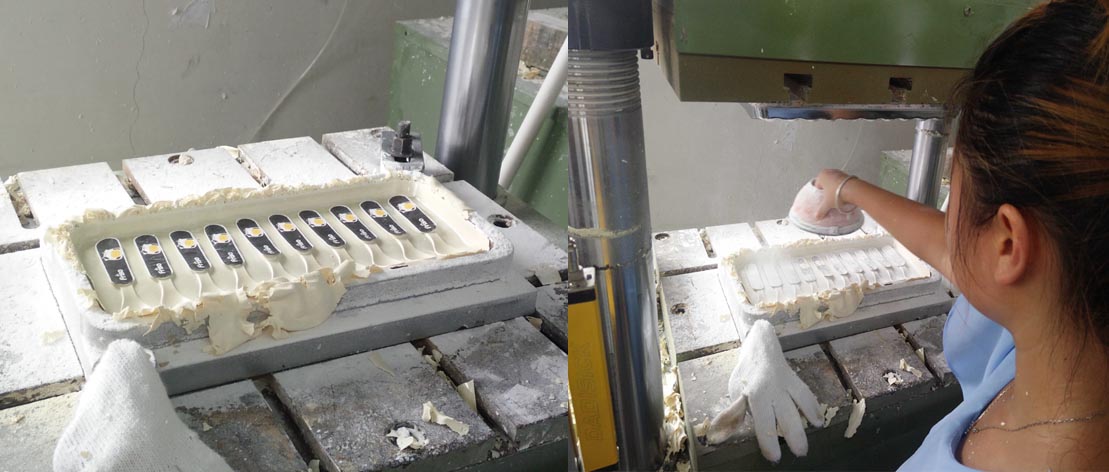
Place the decal in correct position and spray lightness powder
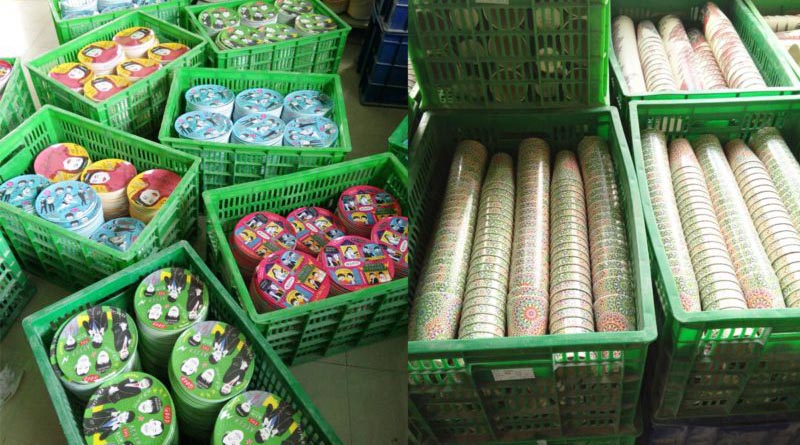
Not finsihed yet…wait for next post to wrap up.
Authored By Mark
